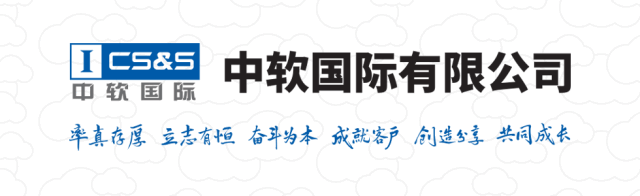
钢铁行业是我国重要的工业基础之一,也是国家经济发展的重要支柱,随着我国经济的快速发展,钢铁行业也不断面临着新的挑战和机遇。2021年底,工业和信息化部等八部门联合发布《“十四五”智能制造发展规划》,要求钢铁企业向智能钢铁工厂转型,从而加速中国新型工业化进程。那么如何通过智能化手段实现生产优化、资源节约、环境保护与提高效益,已成为行业焦点所在。
中软国际结合钢铁行业客户的业务场景,围绕钢铁生产工艺流程(采矿→选矿→烧结→炼铁→炼钢→热轧→冷轧→钢材→物流)中出现的痛点,例如,矿石繁杂品质难控、原料称重效质低下、能耗成本高、管理难、皮带磨损停产待工、钢卷摆放效率低、误差大等,提炼出包括矿石分类定级、无人值守磅站、智能皮带检测、AI安全管理设备管理&预测性维护、AR点巡检管理在内的16个典型业务管理需求。并快速实现了10个以上的应用场景上线,促进钢铁企业的数字化应用落地。
中软国际钢铁冶炼与压延行业智能化应用解决方案,通过运营中心、应用层、平台层、网络层、设备层五个层面的有机结合,构建了一个全方位、多维度的智能化生产体系。此方案不仅强化了生产过程的可视化与可控性,还有助于实现资源优化、减少浪费、提高效益,为钢铁冶炼与压延行业的现代化和可持续发展提供了强有力的支持。运营中心层是整个解决方案的核心管理部分,主要负责对整体业务运营的监控、分析和优化。运营中心通过实时数据分析,确保生产过程的高效与顺畅,并可依据需求灵活调整资源分配。应用层则负责各项业务功能的实现,包括矿石定级分类、综合能耗管理、粉尘含量监测、钢卷包材优化、轧辊最优库存等。通过集成各项技术,实现生产的自动化和智能化管理,促进生产效率与质量的提升。平台层作为中间层,连接应用层与底层设备,提供统一的数据交换和服务调用机制。该层的稳定性与灵活性关系到整个系统的协同效应和可扩展性,是系统集成的关键部分。网络层确保信息在各层之间的无缝传递。采用有线连接、蜂窝连接、非蜂窝连接等网络连接技术,确保数据高速、安全、稳定传输。通过与现有网络设施的无缝集成,可快速响应市场变化,及时调整生产策略。设备层负责与生产线上的各类硬件设备连接,包括但不限于气体传感器、传送带、高炉、冷热轧设备等。通过实时的数据采集与控制,确保生产过程的精确与可控,降低人为干预的风险。中软国际钢铁冶炼与压延行业智能化应用解决方案,可以帮助企业实现从生产管理到质量管理、设备管理、能源管理等全方位的智能化应用,提高生产效率和质量,降低成本,提升企业的竞争力。未来,中软国际将继续深入探索钢铁行业的转型升级之路,为推动行业的高质量发展贡献力量,为企业提供更加先进、高效的解决方案。该客户为国内某全球50强钢铁企业,2022智慧钢城建设优秀企业,年产量1000万吨,年营收1000多亿,员工15000余人。基于“1张网(5GSA企业专网)+1平台(5GMEC平台)+3中台(数据中台、AI中台、管理中台)+N应用(8类面向不同场景下钢铁定制化应用)”模式,实现生产少人化、过程透明化、响应实时化的智造要求,打造智能、节能、高产能的企业数字化管理软体:矿石分类和定级系统:人力成本降低70%,扣杂准确率提升至80%,生产效能提升80%;皮带检测系统:系统从发现撕裂现象到紧急刹车,反应时间由1分钟缩短至5秒,避免大面积皮带划伤;综合能耗管理系统:节省人力60%,综合能耗降低5%,年均节省能耗支出300万+;空气质量(粉尘)监测:粉尘浓度达标率100%,年节约经费25万+;钢表面检测系统:人员缩减80%,识别准确率提升至95%,缺陷提示及时率99%;钢卷包材优化管理系统:包材统计准确率提升至99%,包材管理更规范,工作效率提升70%;拆辊车间钢卷带头联动系统:工作效率提升30%,准确率提升至99%;轧辊最优库存系统:过度磨削率降低90%,重复磨削率降低70%,工作效率提升80%,大大降低库存压力。